Highlights
Stanpol SLR is a kind of paint that has a feature of showing shield specialty against electromagnetical radiation in low and high frequency and isolating radiation by absorbing electromagnetical field in the environment. There is no heavy metals or chemicals that threaten human health within its content.
Stanpol SLR which completely fits the parameters of any nuclear facility flooring. It is completely sealed being monolithic, will not crack under duress not even from steel-wheeled forklifts, and best yet it will last a lifetime. That building is probably going to be there way after nuclear facilities are no longer needed, but that Stanpol SLR flooring will still be there.
SL flooring system for nuclear contamination area and reactor building of NPCIL. Radiation resistance coating for internal lining of reactor building in nuclear power projects, and equipment/structures/concrete floors installed in contaminant area.
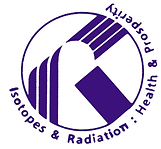



Primer - Staroxy 102 ARSF
-
Mix Part A and Part B of Staroxy 102 ARSF with Electric Stirrer. Once parts A & B have been thoroughly mixed, the product may be thinned to aid application.
-
Apply the primer coat by brush and then roll the centre with a short nap roller.
-
Allow a drying time of at least 4 hours before applying basecoat. If you intend to install epoxy corner coving, this should be done before commencing the next step.

Basecoat - Staroxy SLR UL 1000
-
The base coat used for nuclear radiation resistant flooring is usually Stanpol SLR UL. Mix constituents of Stanpol SLR UL 1000 in a clean bucket with Electric Stirrer according to the instructions on the technical data sheet.
-
Starting at the far corner, apply the basecoat by trowel and roller and evenly broadcast the Sand if necessary, into the wet product until all the basecoat is covered, except at the leading edge.
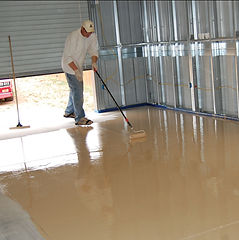
Topcoat - Stanpol SLR 1000
-
The top coat used for nuclear radiation resistant flooring is usually Stanpol SLR 1000. Mix constituents of Stanpol SLR 1000 in a clean bucket with Electric Stirrer according to the instructions on the technical data sheet.
-
Starting at the far corner, apply the basecoat by trowel and roller and evenly broadcast the Sand if necessary, into the wet product until all the basecoat is covered, except at the leading edge.
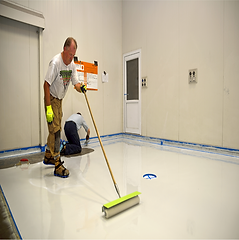
Topcoat - Stanpol SLR 2000
-
It is important to select a suitable topcoat which will meet all the visual and wearing requirements.
-
Mix the topcoat usually Stanpol SLR 2000 as per the instructions. Remove the perimeter tape and protect the floor from full traffic for 7 days.
-
You can take coverage of 5 Sq. Mtr. For 2mm thickness of topcoat.

Roller Topcoat Staroxy SLR 500
-
It is a cost-effective solution for with less thickness of topcoat. It is important to select a suitable topcoat which will meet all the visual and wearing requirements.
-
Mix the topcoat Stanpol SLR 500 as per the instructions. Remove the perimeter tape and protect the floor from full traffic for 7 days.

Other Useful Products

-
Staroxy 20 SF – Sand Coving
-
Aggregates – Sand, Silica Powder, Talc Powder
-
Staroxy 21 WB – Water base Coving
-
Stancrete 33 PU – PU base Coving
-
Stanrocove 25 – Covefinish
-
Staroxy 22 – Epoxy Coving Paint
-
Starothane 23 – PU Coving Paint
-
Starothane Yellow/White – PU Yellow Lining Paint
-
Staroxy Yellow/White – Epoxy Yellow Lining Paint